Moving toward energy efficient textile industry & its importance
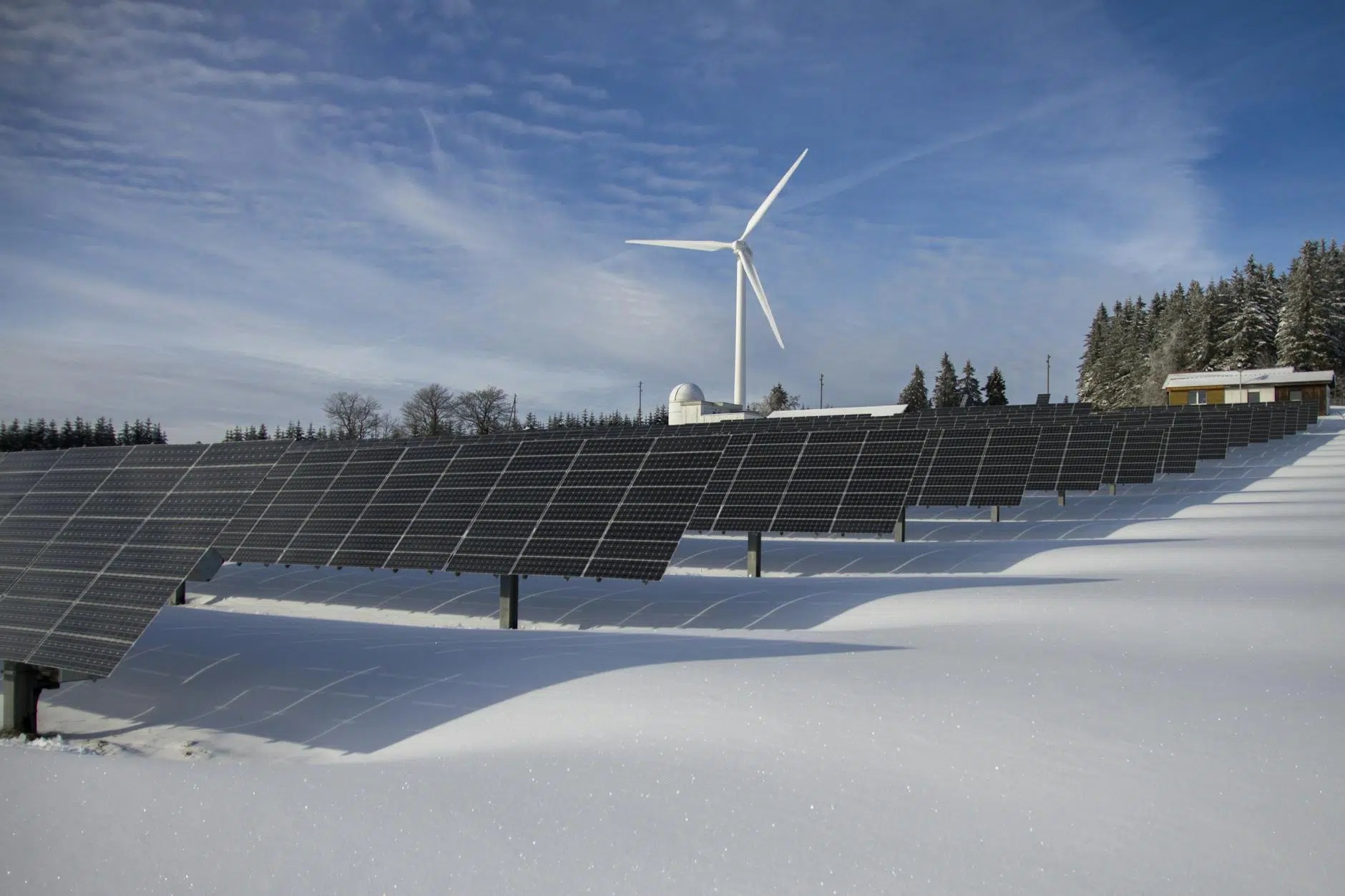
Textile manufacturers are trying to meet the demands of the ever-changing fashion industry. The fast-growing textile industry is one of the most energy-intensive industries, although it holds the record for the least efficiency in terms of energy use. In terms of energy consumption, the chemical processing industry consumes approximately 39% of energy, weaving 22%, spinning 33% and 6% for various purposes. Textile manufacturers need to adopt more efficient means of energy, time, money and production for new designs, materials, etc.
Textile manufacturing is difficult to characterize due to the diversity of machines, processes, materials, finishing steps and functional components. For example, to produce a finished fabric, different types of yarns or fibers, different fabric production methods and finishing processes (mechanical finishing, chemical finishing, printing, preparation, dyeing and coating) are all interconnected.
Due to the variety and intensity of its processes, the textile industry consumes large amounts of energy. Different types of textile industries use different energy sources. For example, in wet processing fuel is the main energy source, while in yarn spinning electricity is the main energy source. However, saving energy is no longer a luxury but a necessity.
There are two main ways to make the textile industry energy efficient. One is to retrofit or optimize processes, the other is to replace old machinery with modern, sophisticated, and efficient technology.
How to make textile industry energy efficient
All sectors of the textile industry are involved in energy management. First, it is important to analyze the lighting usage. As this is an important factor in electricity consumption, it is important to analyze whether the light source is used efficiently and take conservation measures. Limiting the use of light, incorporating daylight conservation policies, using solar energy, and using energy-saving lights etc. can be good options to save energy.
Electric motors use a lot of energy. Conventional machines use a single motor to generate mechanical power, which is then transmitted to all parts of the machine. Modern technology now includes several small motors that are connected to the machine and have a control board that controls the movement of the motors.
Fuel selection, including high calorific value, gas properties, ease of combustion, etc., is an important issue to consider. Changing boiler technology is also a smart way to make your industry more energy efficient.
Although the textile industry does not require large amounts of steam, significant losses occur while transporting steam due to thermal radiation in pipelines. In addition to steam pipes, steam accumulators must also be considered. This is because a steam accumulator is installed in the middle of the heat transfer pipe, between the boiler and the load that stores excess steam and receives heat. It helps save excess steam by converting steam into hot water.
Almost all applications in the textile industry require frequent heating and cooling of liquids and gases that act as heat media. Heat exchangers are useful during heat exchange between different fluids to ensure that direct contact does not cause chemical reactions or contamination. Heat exchangers ensure efficient indirect cooling and heating of these liquids and gases.
Above all, with constantly changing fashion trends and the requirements of the textile industry, energy audits are essential for energy saving and conservation. Energy auditing is a study that analyzes and inspects the flow of everything used in industry. This helps reduce the amount of power input to the system without negatively affecting output.
Additionally, through periodic maintenance and timely preventive measures, the industry is significantly reducing power consumption. A well-maintained machine provides better power output while consuming less fuel, electricity, or other energy sources.
Alternative Energy-Efficient Processes
Every year the United Nations holds a World Climate Conference. According to the decision taken at the climate conference held in Paris in 2015, the use of renewable energy instead of fossil fuels will be ensured worldwide by 2030 to combat climate change. For that purpose, energy conversion, energy conservation and efficiency improvement and the use of renewable electricity in transportation, agriculture, industry, commerce and residential are increasing in countries.
Instead of using conventional energy, textile industries today are switching to other non-conventional energy sources including solar energy, geothermal energy, wind energy, tidal energy and biomass. Initially, people used solar lights for appliances that required minimal power. However, modern solar panels are robust, stronger and can provide more power. Many textile manufacturers are powering their production units through solar energy.
Fossil fuels are rapidly being replaced by renewable fuels in grid electricity generation. In 2021, an average of 10 percent of the world’s electricity generation came from renewable energy.
Importance of energy efficient textile industry
Textile is a highly competitive industry. To be competitive, one must find ways to reduce production costs without affecting product quality. Continuous increases in price lead to increase in cost of production. Hence, energy conservation has become imperative to stay afloat in the competitive industry.
Improving energy efficiency should be one of the main concerns of the textile industry, especially in times of high volatility in electricity prices. Because energy is one of the major cost factors in the textile industry. Every single penny matters. Energy engineers can have a significant impact on the bottom line of textile companies by applying various techniques and technologies, such as upgrading to more efficient equipment, improving insulation, and implementing waste heat recovery systems.